Reconnu pour leur robustesse et leur fiabilité, les lampadaires solaires Fonroche Lighting sont les seuls à garantir 365 nuits d’éclairage par an, par tous les climats, sur tous les continents. Grand vent, chaleur ou froid extrême, variation de températures, corrosion, humidité... les lampadaires sont mis à rude épreuve !
Afin de garantir la haute résistance et l’efficacité de nos systèmes et produits, nous avons déployé des expertises en test & validation, comprenant un laboratoire d’essais batterie de plus de 500 m² avec la plus grande capacité de tests batterie dédiée à l’éclairage solaire au monde.
Un laboratoire de test batteries unique au monde
Fonroche Lighting fabrique ses propres batteries Power 365 sur son site de production situé dans le Sud-Ouest de la France. Afin de garantir la haute performance de notre système de stockage, nous avons créé un laboratoire d’essais de batteries, comprenant un parc d’enceintes climatiques permettant de simuler tous les climats, spécialement dédiée à l’éclairage solaire.
500.00
M²
d'espace dédié
12.00
Enceintes climatiques
10.00
Bancs de cyclage
1300.00
batteries par an (en capacité d'essais)
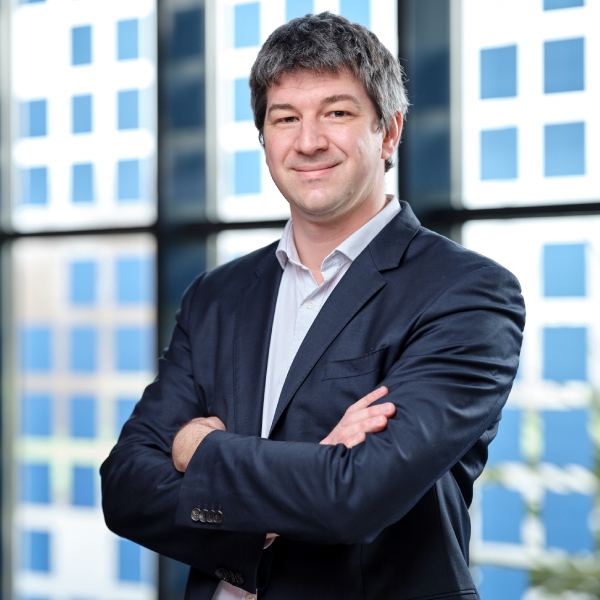
Benoît Arsac
Directeur R&D
La garantie d’un lampadaire solaire n’est pas une simple ligne écrite en bas d’un contrat ! Ce sont bien des produits éprouvés en laboratoire qui suivent un cycle d’essais très sévère, avant d’être autorisés à être mis sur le marché par notre exigeant service qualité.
Simuler tous les environnements climatiques pour une performance optimale
Entièrement dédié aux essais batteries, ce laboratoire à la pointe de la technologie dispose de plusieurs dizaines d’enceintes de simulation d’environnement climatique.
Elles permettent de réaliser des essais sur les batteries et modules afin de simuler tous les climats existants sur la planète, et de les soumettre à des tests sévères allant au-delà du réel, pour garantir la fiabilité, la résistance et la longévité de nos systèmes.
Ses simulations climatiques permettent de chercher les limites ultimes des batteries en incluant :
-
Caractérisation du comportement des batteries sur tous les climats,
-
Vieillissement accéléré - caractérisation et confirmation de la durée de vie des produits
-
Chocs thermiques, variations rapides de températures (10°C/mn)
-
Étanchéité
-
Corrosion, brouillard salin, etc.
Ce ne sont pas moins de 40.000 heures de tests cumulées qui sont nécessaires pour valider un nouveau type de batterie ou une de ses évolutions.
Des compétences pointues en test, validation et prototypage.
Au-delà des batteries, les autres composants subissent également de nombreux tests et validations.
Fonroche Lighting a constitué une équipe dédiée ayant pour objectif de garantir la qualité et l’aspect fonctionnel des batteries, des panneaux photovoltaïques et des LED’s et surtout assurer une performance optimale avant de les déployer sur le marché.
Un processus de validation en 4 étapes principales est mis en place pour tester et valider ses composants :
Chaque fournisseur de matière première nous fait parvenir le prototype d’un composant qui répond à nos spécifications, pour que nous puissions faire une caractérisation.
Par exemple, pour les cellules de stockage, elle consiste à tester la :
-
Capacité de la batterie
-
Résistance interne
-
Efficacité de charge
-
Auto Décharge
-
Usure calendaire, etc...
Le test le plus important dans la caractérisation de la batterie est le cyclage qui permet de déterminer sa durée de vie. Plusieurs types de cyclages sont testés dont 3 principaux :
-
Cyclage Standard
-
Cyclage Accéléré
-
Cyclage Spécifique au Solaire (Respectant la norme IEC 61427-1)
Chaque composant a ses propres tests spécifiques, spécialement pensés pour l’éclairage autonome. Les produits sont testés dans leur ensemble dans des conditions climatiques extrêmes (Corrosion, brouillard salin, humidité, vibration, soufflerie, CEM - compatibilité électromagnétique) afin de garantir leur fiabilité et leur résistance.
A réception des échantillons, nous testons les aspects globaux comme l’aspect dimensionnel et les performances. Ces échantillons initiaux font référence pour la production de masse qui en découle.
Tous les composants sont validés dans des conditions de laboratoire.
Nous faisons un pré-déploiement sur une quantité élevée de lampadaires dans des climats différents et assurer un suivi qualité, pour que les performances soient optimales dans des conditions réelles.
C’est la dernière étape pour s’assurer de l’aspect fonctionnel du lampadaire. Tous les composants sont ensuite certifiés.
Lorsque toutes les étapes sont passées avec succès, nous déployons les lampadaires solaires sur le terrain. Pour garantir une qualité dans le temps du lampadaire, un test destructif est réalisé sur chaque lot.
Ce processus strict et complet est appliqué immédiatement lors de chaque intégration d’un nouveau composant, ou lors du lancement de nouveau produit.
Les équipes Fonroche Lighting réalisent également des processus de validation adapté sur nos logiciels embarqués, présents dans notre technologie Power365, comprenant des tests de transition jour/nuit, de programmation, de profils d’éclairement suivant les différents climats, afin de vérifier l’ensemble des fonctionnalités du lampadaire.
Processus d'amélioration continue
Pour augmenter la compétitivité de nos solutions, nos équipes sont engagés dans un processus d’amélioration continu, comprenant des retours d’expérience, des tournées d’inspection sur le terrain et une surveillance continue, grâce à nos logiciels de monitoring à distance.